The BlockageAnalysis of Screw Conveyor
The
screw conveyor is mainly composed of driving device, head section, standard middle section, optional section, tail section and spiral shaft blade.In addition to the head and optional sections, the casing and spiral joints are interchangeable.When spiral blade is rotating, the blade push material along the conveyor moving forwardcircular bottomgroove,so inside the casing, materials are deliveried forward according to the order, smooth and evenly to where it is needed.
.jpg)
Screw conveyor is a kind of continuous conveying machine for conveying bulk materials in short distance or vertical.Its main features are: simple structure, small dimension, low cost, good sealing, it can realize the multipoint discharge, mixing effects for the material, but its transportation distance is small, blade and casing is easy to wear, high energy consumption, crushing effect of materials is strong.
Thescrew conveyor is sensitive to materials because of the small space of conveying materials.The winding of the coil is easy to occur when the screw axis is rotating;there are also intermediate hanging bearings easy to clog the material.Therefore,
blockageis the most common failure of the screwconveyor, which can affect the output and increase the power consumption. In severe cases, the motor will be burnt, and the screw axis will be broken to affect the normal production.There are many reasons for blockage, and the following measures can be taken to prevent blockage:
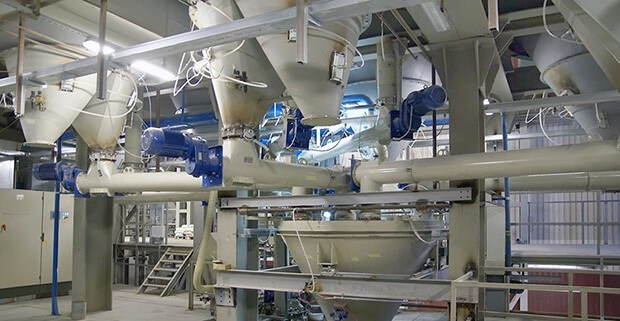
1.Choose the technical parameters of
screw conveyorreasonably , such as the speed of slow screw conveyor cannot be too large.
2.Strictly enforce the operating procedures, without load starting and no-load parking;Ensure continuous and continuous feeding.
3.To increase the feeding or extension the feeding end, to solve the problem of unsmooth discharge or out of time dischargematerial.At the same time, a small counterrotating blade can be installed at the end of discharge opening to prevent the end block.
4.It is necessary to clean the material entering the conveyor to prevent the large or fibrous impurities from entering the machine to cause blockage.
5.The transverse dimensions of the intermediate suspension bearings are minimized to minimize the possibility of material passing through the intermediate bearings.
6.Install the bin material position instrumentand plug the sensor to realize automatic control and alarm.
7.Set up a door on the discharge end of the cover plate.When blockage occurs, due to the accumulation of materials, the door is open and the power is switched off by the travel switch.
Further information,please click:
www.pkmachinery.com